Hydrogen Embrittlement in Welded Rebar
- Timothy Kenney
- Aug 30, 2016
- 4 min read
The infrastructure surrounding a reasonably large grocery store was being evaluated for final acceptance. A truck driver with a low bed trailer was attempting to leave the parking lot at a very slow and cautious speed, however while backing he tapped a light fixture supported by a concrete foundation. Even though the impact was only a slight bump, of the light fixture broke as if it were a 20″ diameter piece of brittle glass. This was witnessed by the group working on accepting the final completion short list. Needless to say the short list just got longer.
Examination on site showed that the fabricator had produced a welded steel cage that could be lowered intact into the long vertical steel molds. The rebar cage was spot welded to the stirrup. Visual observation showed the vertical steel reinforcement to have conchoidal fractures which are not representative of ductile steel. Upon additional inspection, it was noted that all fractures occurred at or in the immediate vicinity of a welded junction of the stirrup and the longitudinal reinforcement bars. This was also true of the failed anchor bolts which failed at the washer welds.
Steel samples were removed for tensile testing and chemical analysis.
Tensile test specimens from the rebar samples (ASTM E615 steel) were prepared and tensile tested per ASTM E8.
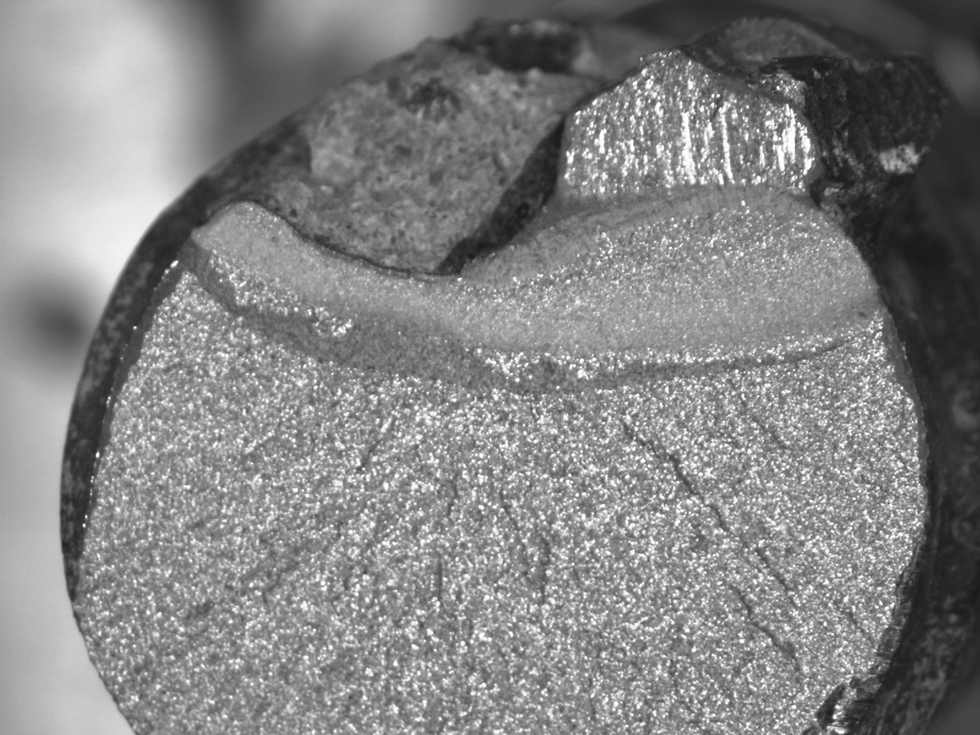
Chemical analyses of the rebar samples, and of an accident fracture, were performed using glow discharge spectroscopy. A chemical analysis of one fractured anchor bolt (B1) was also performed. These results are summarized on the below table
Summary of Chemical Analysis and Mechanical Testing Results
0.2% Yield (ksi) 73.0 72.9 73.0 72.3
Tensile (ksi) 111.7 109.7 113.8 114.5
% Elongation 22.5 24.5 26.9 24.4
Composition (Wt%)
C 0.46 0.42 0.43 0.44 0.47 0.47
Mn 1.08 0.92 1.09 1.09 0.83 1.05
P 0.027 0.010 0.023 0.025 0.040 0.029
S 0.035 0.036 0.035 0.035 0.024 0.086
Si 0.16 0.17 0.16 0.16 0.28 0.18
Cr 0.18 0.15 0.18 0.18 0.01 0.18
Ni 0.13 0.13 0.13 0.13 0.01 0.13
Cu 0.33 0.31 0.34 0.33 0.01 0.33
The tensile test specimen with a heat affected zone in the center of the reduced area showed less ductility, 19.8%, compared with the previous tests. The test specimen fractured away from the center of the reduced section which contained the harder heat affected zone. Accordingly the test results do not show the full effect of the diminished ductility.
The three rebar samples marked “cut” had fracture surfaces adjacent to welds. In each sample the fracture initiated in the heat affected zone adjacent to the weld. A longitudinal metallographic specimen was prepared through the fracture surface of rebar specimen. Photomicrographs of the cross-section are pictured here at 10x magnification.

This photograph of a metallographic cross section of this fracture shows the fracture initiated in the heat affected zone adjacent to the weld. The hardness in the heat affected zone is HV (1000g) 571, or approximately HRC 53.6. This HAZ is harder than the lab fractures summarized above. The microstructure of the heat affected zone is fully martensitic.
Vickers (1000g) microhardness tests were performed on the cross-section and these results, with conversions to Rockwell C values, were as follows:
Summary of Vickers Hardness Tests
Location HV HRC
Weld 241 20.6
HAZ 1 (adjacent to weld) 339 34.3
HAZ 2 (brown colored) 495 48.8
HAZ 3 (adjacent to base metal) 361 36.8
Fracture Surface (center) 157 82.3 (HRB)
Base Metal 232 98.7 (HRB)
Scanning electron microscopy was also used on one of the fracture surfaces. The fracture initiation zone shows brittle intergranular fracture. The final fracture is primarily transgranular cleavage. The intergranular fracture in the fracture initiation area and the transgranular fracture in what should be ductile base metal are characteristic of hydrogen embrittlement.
The accident rebar sample was examined in a similar fashion. The fracture on that sample also initiated in the heat affected zone of the adjacent weld. The fracture surface was sufficiently battered so that electron microscopy did not reveal significant information.

SEM image of fracture initiation. Note the intergranular fracture due to hydrogen embrittlement.
The rebar samples have a carbon equivalent of approximately 0.66. Steels with a carbon equivalent of greater than 0.475 require preheating before welding to prevent hydrogen induced cracking. The preheating reduces the cooling rate of the heat affected zone and provides a more ductile microstructure that is less susceptible to hydrogen cracking. The slower cooling also allows more time for hydrogen to diffuse out of the weld. The combination of high carbon content and relatively high hardenability of the rebar samples suggests that in addition to preheating post weld heating would also be appropriate.
It has been determined that the root cause of the fractures was to be hydrogen embrittlement from the welding. Note 1 of ASTM A615 states:
“Welding of the material in this specification should be approached with caution since no specific provisions have been included to enhance its weldability. When steel is to be welded, a welding procedure suitable for the chemical composition and intended use or service should be used. The use of the latest edition of ANSI/AWS D 1.4 is recommended. This document describes the proper selection of the filler metals, preheat/interpass temperatures, as well as, performance and procedure qualification requirements.”
As the cause of the observed brittle fractures was due to hydrogen embrittlement from the welding, no determinations of the ductile-brittle transition temperature were performed.
If you would like to view a PDF version of this post please click here.
If you have any questions regarding this topic, please don’t hesitate to contact us at info@nhml.com or you can call on our toll free number 800-334-5432.
Comments